The wax models are constructed, then placed in special tanks that contain thermosetting resins and ceramic granules. These latter together polymerize, creating a resistant outer coating. When the mold is getting cast, the wax melts and comes out of the shell, leaving only the piece to solidify.
Induction Furnaces for Precision Casting
Precision Casting (also called “Investment Casting”) is the modern derivation of the ancient lost-wax casting process. The use of mechanization and automation systems has allowed modern industries to use this casting technique for the production of mechanical components on a large scale.
Medium Frequency Electric Induction Coreless Furnaces for Precision Casting
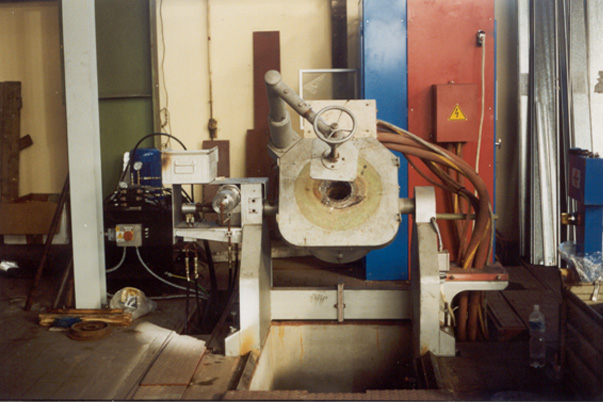
“Roll-Over”-type Medium Frequency Induction Coreless Furnace
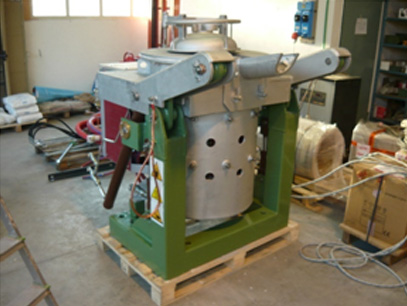
Gravity Medium Frequency Induction Coreless Furnace
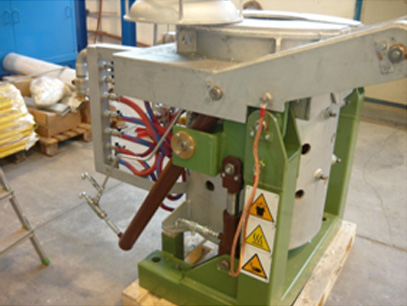
Gravity Medium Frequency Induction Coreless Furnace
IGBT (Insulated Gate Bipolar Transistor) Technology for Medium Frequency Induction Coreless Furnaces for Precision Casting
GMS designs and manufactures IGBT Converter Units with the IGBT Technology ranged from 40 to 4.000 Hz and the output power up to 15 MW, specially designed for feeding of Medium Frequency Induction Coreless Furnaces for Precision Casting.
GMS IGBT Converters are designed to ensure:
- Harmonic index lower than the maximum limits envisaged by current legislation.
- Optical fibre data transmission.
- High Machine efficiency (Energy Saving).
- Remote control of the Machine via the Internet.
- Lower CapEx.
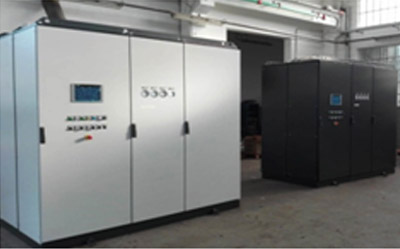
IGBT Technology for Precision Casting Furnaces
Latest News